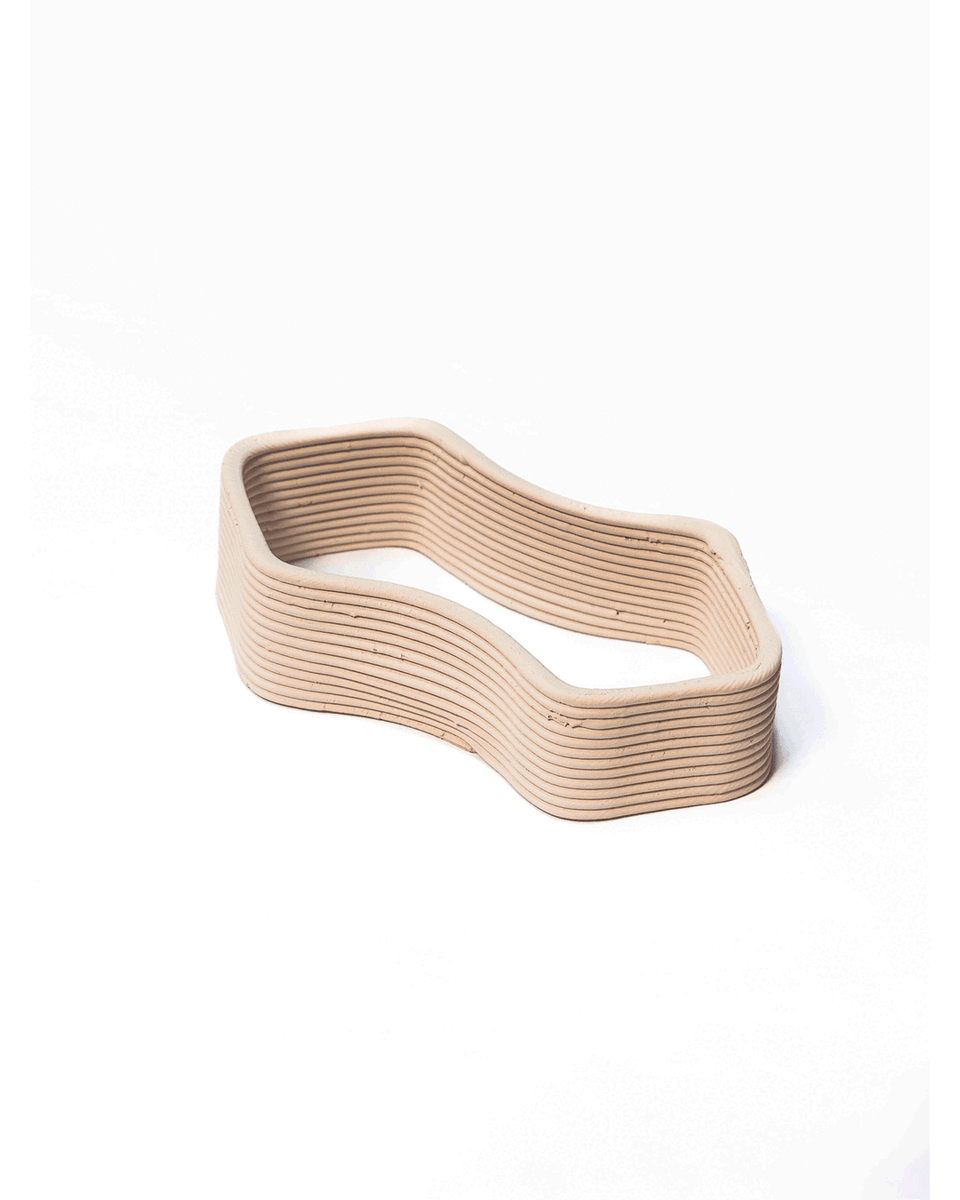
Architecture, understood as a cultural product, is strongly influenced by diverse stimuli that include historical, geographical, and cultural aspects, among others. Together, these elements form a heritage that may (or may not) endure through time. Although architecture tends to adapt to each culture, modeling its traditional techniques according to its context and shaping the surrounding environment, there is no guarantee that the traditional elements in it will endure or remain unchanged over time. This is largely due to the constant evolution of society and technology, which sometimes tends towards universality and the adoption of a common language, rather than one of their own.
Given this scenario, it is essential to explore an approach where innovation and technology do not replace tradition and artisanal production; instead, they arise as a means of exploration towards emerging routes. Adopting novel techniques and innovative materials that are adapted to specific local needs makes it possible to maintain an authentic expression that responds to the demands of the environment. This approach, which could be termed neo-craft, allows for the preservation of a distinct voice that reflects the authenticity of the local context. At the same time, it contributes to a universal perspective, merging the local with the global.