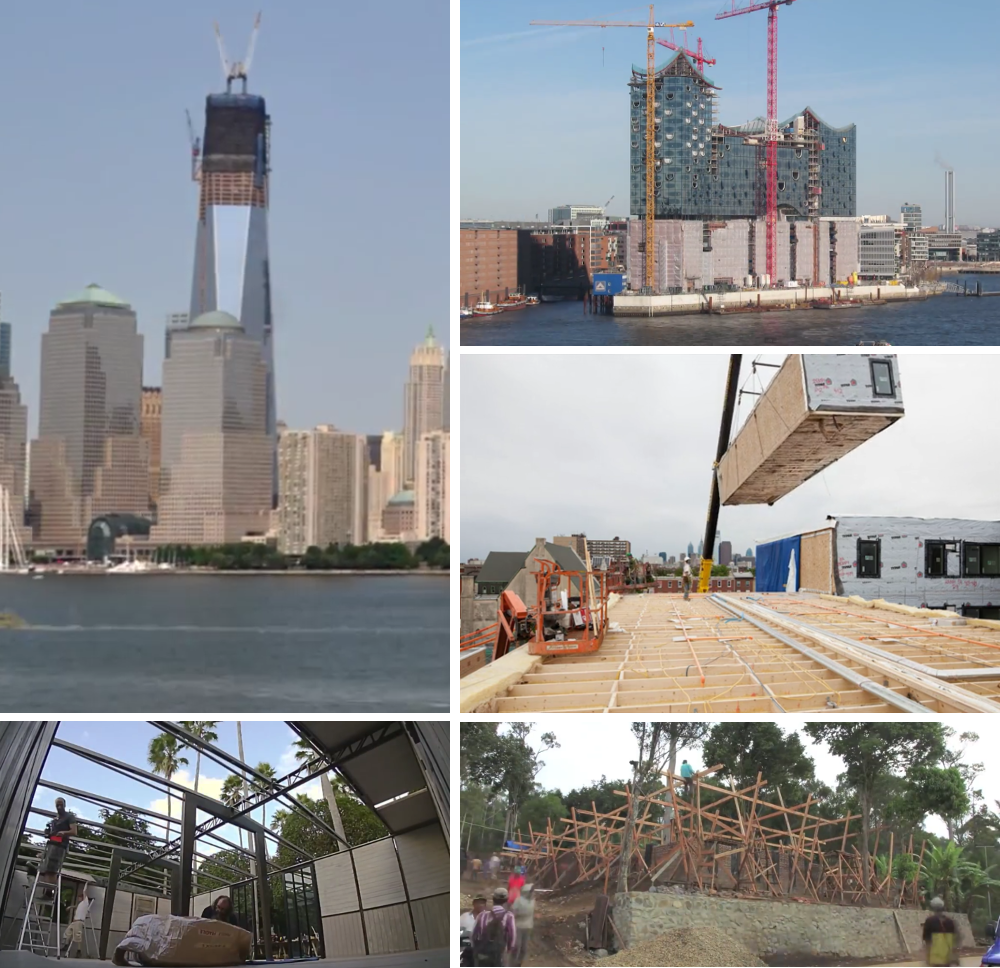
Designers are trained to consider the context for a finished building, but often neglect to consider the construction phase. When architecture is primarily judged based on the impacts it has on their surroundings once they are built, what can be learned from the process of building? The time-lapse is a method that can help architects to do just that, as it can capture years of complex development in a matter of minutes. This can uncover patterns of impact on social and economic levels, as months to years are played back over several minutes.
What is shown by time-lapse videos, though, can be as disturbing as it is interesting; when uncovered, the construction process is a revealing process, and the ramifications in regard to energy consumption can be as monumental as the buildings themselves. The time-lapse allows the viewer to get a better understanding of the types and amounts of materials being put into the construction of buildings, and the impact construction has on its immediate surroundings. By comparing time-lapse videos of different projects, what insight can we gain about how the physically generative process of architecture affects people and place?
Project: Jean Prouve’s Demountable House
Primary Designers / Architects: Jean Prouve / Bally
Dates of Construction: 1 December 2014 - 4 December 2014 (5 days)
Location: Art Basel, Miami, Florida
Material Source: Local and Foreign
Size: 600 square feet (55.7 square meters)
Jean Prouve’s Demountable House is an early example of prefabricated housing. In this method of construction, people with little experience in construction can take part in assembly, and have the entire construction completed with short notice in a wide variety of locations. With architectural projects such as this, the precise location is out of necessity, variable; the original demountable house was designed to provide housing for French citizens whose homes were destroyed in bombings. This method allows for immediate production on a wide variety of terrain, with little to no damage to its immediate surroundings in regard to infrastructure or communal displacement.
Project: T-30A: 30 Story, Five-Star Hotel
Primary Designers / Architects: Broad Group
Dates of Construction: 2 December 2011 - 17 December 2011 (15 days)
Location: Hunan Province, China
Material Source: Local and Foreign
Size: 183,000 square feet (17,000 square meters)
The world was astonished when the T-30A high rise building was revealed, given its unprecedented construction speed. The method that gave rise to this success, like the Demountable House, was pre-fab design and construction. The building itself was designed by Broad Group to not only be composed of identical structure and system modules, but to strive for energy conservation, and to be able to withstand earthquakes of a 9.0 magnitude. The compartmentalization of each component translated into a homogenous structural matrix, which allowed the building to be built astoundingly fast. The time-lapse, though clarifies the construction’s impact on its immediate environment. While the final product may have noble energy-usage considerations, the site had to be completely leveled, displacing tons of natural soil. The construction process was the fastest and most efficient the world had seen at that point (relative to its size), but at what cost does such a scale of construction warrant the alteration of such a substantial amount of earth? As Broad Group develops their technology, they may find a solution.
Read more about the T-30A Highrise here.
Project: Burning Man Pop-Up City
Primary Designers / Architects: Burning Man (Organization)
Dates of Construction: roughly 6 weeks for set-up, execution, deconstruction and environmental restoration
Location: Black Rock City, Nevada
Material Source: Local and Foreign
Size: 5 square miles (13 square kilometers) at 2008 Burning Man
An often overlooked feat of architecture and urban planning, the Black Rock City at Burning Man in Nevada, USA presents a wild look at the intuitive and collaborative nature of humans as designers and planners. Over the course of six weeks, an elaborate volunteer effort drives the construction, habitation, and deconstruction of a city in the middle of the desert. Most people bring their own tents and structures, but upon ending the event, it is customary to “leave no trace,” rendering the site as uninhabited as it was when builders arrived six weeks earlier. This is drastically different from the T-30A highrise in regard to its relationship with the site. Yet both the previous pre-fab constructions are similar to Black Rock City, involving the import of pre-designed, semi-completed components. Doing so proves to be a faster means of construction, which leads to less time altering materials on site.
Project: Public Farm at MoMA PS1
Primary Designers / Architects: Work AC
Dates of Construction: 7 April 2008 - 17 June 2008 (2 months, 11 days)
Location: MoMA PS1, Long Island City, New York
Material Source: Local
Size: 3000 square feet (278 square meters)
PF1 (Public Farm One) was an urban farm concept built with inexpensive and sustainable materials that were intended to be recycled after its installation and use. While the project in its final stage was a lightweight and innovative system to create shaded multi-use public space, the time-lapse exposes how its construction required large quantities of wood bracing as preliminary support. This could be interpreted as antithetical to the initiative; supporting a lightweight structure with almost twice as much initial framing and weight might alter the perspective of those who saw it as an elegant idea about cardboard construction and public gardens. The cardboard tubes were prefabricated, but the preliminary wooden framing was not. And while the final form does have a delicate relationship with the ground, the construction process was more crude. PF1 could have benefited from the methods of Jean Prouve’s Demountable House or even the T30A tower, as more comprehensive pre-fab components could have led to a smaller footprint and lower complexity of construction.
Read more about Public Farm 1 at MoMA PS1 here.
Project: Masoro Village Project
Primary Designers / Architects: GA. Collaborative
Dates of Construction: June 2013 - September 2013 (4 months)
Location: Masoro, Rwanda
Material Source: Local
Size: 925 square feet (86 square meters)
This house designed by GA Collaborative was built as a prototype for developing construction methods in Rwanda. Using local labor with educational incentives, this project aimed at empowering its clients with knowledge of an inexpensive and speedy construction technique that involved the local community and used local materials. The primary building method of Earthbag construction acted as a hybrid of pre-fab and on-site production. Unlike the T30A highrise, displaced earth was immediately integrated into a fundamental component of structure, insulation and aesthetic. Through its holistic means of construction, the Village Project even hoped to empower the builders to initiate their own constructions in the future, using the skills they had developed. Men, women and children collaborated to make the building emerge from the local materials around the site. The scale of this construction also allows us to understand the simple but fundamental building principles prevalent in Earthbag construction. While fabrication may not be pre-construction, it is immediately produced and used on site, allowing the architecture to grow from the hands of the community that will benefit from it.
Read more about the Masoro Village Project here.
Project: Cassia Coop Training Centre
Primary Designers / Architects: TYIN Tegnestue Architects
Dates of Construction: August 2011 - November 2011 (4 months)
Location: Sumatra, Indonesia
Material Source: Local
Size: 6,450 square feet (600 square meters)
Designed as a local training school for children and professionals in the Sumatran Cinnamon industry, the Cassia Coop Training Centre makes use of local materials, local labor, and local ideas. Its construction used locally crafted bricks and spare wood from the harvesting of cinnamon, making it an incredibly cost-effective construction that did not impede on the local aesthetic. Its lightweight construction and all-wood roofs allow it to be highly flexible and minimally harmful in the event of an earthquake. The time-lapse of the Cassia Coop construction reveals construction methods similar to those of more developed countries, using concrete foundations and specifically articulated masonry walls, yet the open floor plan and local production of materials allows this construction - like the Masoro Village Project - to emerge from the local surroundings, even if the design itself does not.
Read more about the Cassia Coop Training Center here.
Project: The Modules Student Apartment
Primary Designers / Architects: Interface Studio Architects (ISA)
Dates of Construction: 2009 - 2010 (14 months)
Location: Philadelphia, Pennsylvania
Material Source: Local and Foreign
Size: 80,000 square feet (7,430 square meters)
As a reflection of the competitive student housing market, The Modules embraces prefabricated building techniques to the extreme. The building is the largest wood-frame modular project in Philadelphia, and one of the largest pre-fab multifamily structures in the US. Using pre-constructed units, ISA’s time on site and the overall time-cost of transportation of materials was cut in half. Compared to the pre-fab projects discussed earlier, this made use of the most complete housing modules, and in the timelapse, the brick-by-brick construction method is blown up to a larger scale than that of the Demountable House or the Public Farm. However, it is clear from the video that once the modules were assembled there was still a significant amount of construction to be done on the building as a whole, potentially calling into question the claimed efficiency of pre-fab design today.
Read more about The Modules here.
Project: The Truffle
Primary Designers / Architects: Ensamble Estudio
Dates of Construction: 2006 - 2010 (5 years)
Location: Costa da Morte, Spain
Material Source: Local and Foreign
Size: 270 square feet (25 square meters)
It may come as a surprise that The Truffle, being an object of architecture less than 300 square feet (28 square meters) in habitable size, took more time to make than all aforementioned projects combined. The form was produced by surrounding a mound of hay with a substantial amount of concrete, supported by walls of earth from the immediate site. As you can see in the time-lapse, after this initial construction period, the architectural development of the central space was significantly slowed by the day-by-day excavation of a small calf. Over the duration of the calf’s life, the interior space was slowly revealed, and upon its clearing, further construction developments could occur. While the methods of construction and detail installation were (comparatively) conventional, the process by which Ensamble Estudio chose to reveal The Truffle’s space was anything but. The building itself exists on the border of a developed community and an open landscape. In most buildings the construction process is a means to an end, but The Truffle shows that if the physical generative process itself is explored, new opportunities may emerge. The desired end product could still be architecture, but it could also be a full-grown cow.
Read more about The Truffle here.
Project: Elbe Philharmonic Hall
Primary Designers / Architects: Herzog & De Meuron
Dates of Construction: April 2007 - estimated October 2016 (9 years)
Location: Hamburg, Germany
Material Source: Local and Foreign
Size: 1,291,670 square feet (120,000 square meters)
Above a 17th century factory, an enormous building dedicated to the music industry of Germany has been under construction since 2007. After going five years past the projected completion, this feat of architecture and planning is yet to be completed. Footage of construction provides a different perspective on the relationship to site. The original building was gutted out, and filled with new construction, while the majority of construction materials and machinery inhabited the original footprint of the building. This may have been one of the strategic moves to minimize negative impact on the surroundings, but may also have contributed to its delayed completion. As explored in the videos above, constructing meticulously has both advantages and disadvantages.
Read more about the Elbe Philharmonic Hall here.
Project: One World Trade Center
Primary Designers / Architects: Skidmore, Owings & Merrill (David M. Childs)
Dates of Construction: October 2004 - Memorial Day 2015 (11 years)
Location: New York City, New York
Material Source: Local and Foreign
Size: 3,501,274 square feet (325,279 square meters)
The longest-term construction on this list, One World Trade Center is the tallest tower in the Western Hemisphere. What can be seen from the time-lapse is a focus on its growth upwards, indicative of its main feature: height. And though the the construction process itself is a stability-driven, private enterprise, it nevertheless demonstrates how the release of regular updates to the public reflects a relationship of performance and spectator - a relationship New York City is quite familiar with. The process of construction, however arduous, was considered by many in New York City as an event of social and political significance. While One World Trace Center does not deal explicitly with pre-fab construction, locally-sourced material, or deconstruct-able systems, it does demonstrate how initiatives of construction can play deep-seated social roles in the location it is erected in.
Read all of our coverage of One World Trade Center here.
Should the construction of architecture have as great a social impact as the building itself? Or should the act of building be an educational one that has effects that go beyond the built structure? There may be as much to learn from a tower that can be assembled in 15 days, as a city that can appear and disappear over the course of a month. For too long, architecture has been judged as a final object rather than a process - as a product rather than a limb of a larger system. If the generative process of an architectural idea can have just as great effects in its construction as in its final form, then the fields of design and architecture may benefit from expanding the idea of what architecture can do, before it’s even open for business.