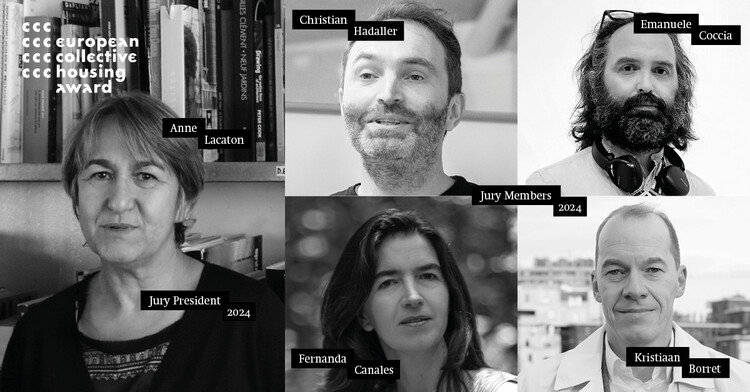
Architectural awards serve as a fundamental platform within the profession and the wider community. They recognize and celebrate outstanding achievements in architectural projects, promoting excellence and innovation, while also providing visibility and exposure for architects and companies, highlighting projects that might otherwise go unnoticed. This impact is particularly evident in collective housing projects, which face a range of challenges, from issues of cost and compliance with urban planning legislation to the need to create welcoming and functional environments for residents. By highlighting diverse initiatives and approaches, awards inspire and educate, stimulate dialogue and the exchange of ideas, and contribute significantly to the advancement of architecture by recognizing projects that address specific themes such as sustainability or social impact.