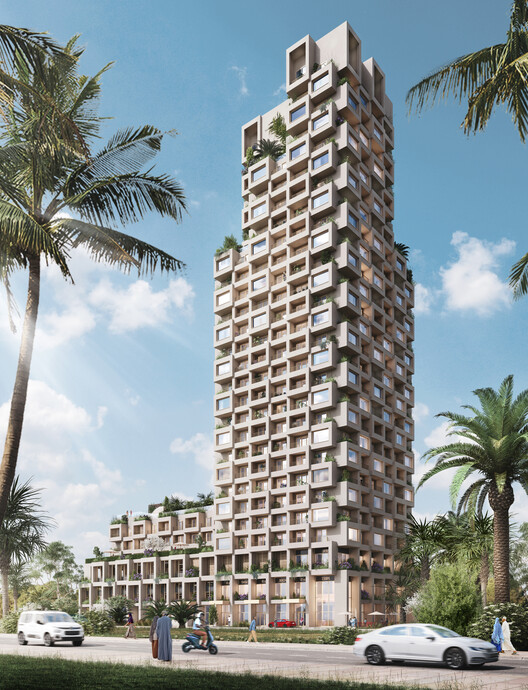
German-based architecture firm OMT designed Africa's tallest hybrid timber tower in Zanzibar City, Tanzania. In partnership with Birk Heilmeyer Frenzel Architects, engineering firm Knippers Helbig Advanced Engineers, and CPS Developers, the "Burj Zanzibar" will rise 96 meters tall to accommodate 266 residences and recreational and conferencing facilities. The mixed-use tower will promote the locally available wood and support the growing urban infrastructure that, according to the government plans, expects to attract tech companies to turn the island into a leading hub for Africa's technology companies.