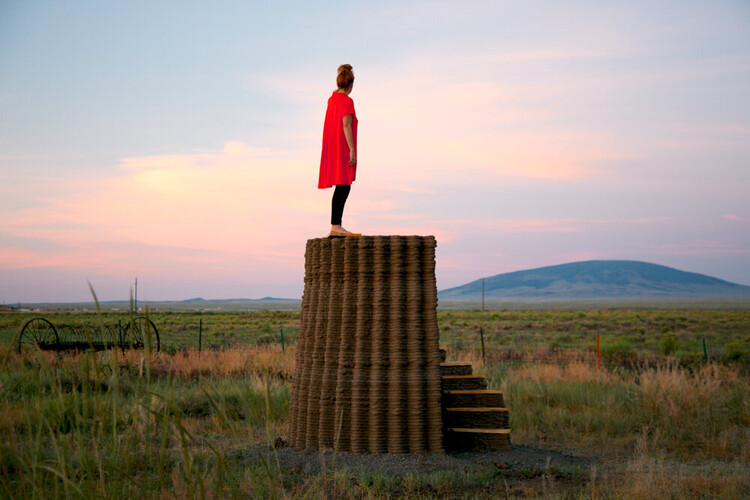
Understanding a discipline from multiple perspectives and intersections is essential for acquiring a deep understanding of it. In architecture, the diversity of approaches to its study enriches our perception by allowing us to appreciate its complexity from different angles. For students and professionals alike, exploring aspects such as history, sources of materials and products, construction processes, implementation of new technologies, and contemporary social challenges is crucial. These aspects intertwine and expand the conventional notion of "architecture," transcending the mere creation of buildings or the definition of spaces.
Ronald Rael, an architect and the Eva Li Memorial Chair in Architecture at the University of California, Berkeley, exemplifies this vision through his practice, which spans from research to connecting indigenous and traditional material practices with contemporary technologies and issues. As an activist and designer, Rael's research interests explore additive fabrication, border-wall studies, and earth construction. Co-founder of Rael San Fratello, Emerging Objects, and Forust, his practice shows an approach to architecture that is highly relevant in contemporary times.