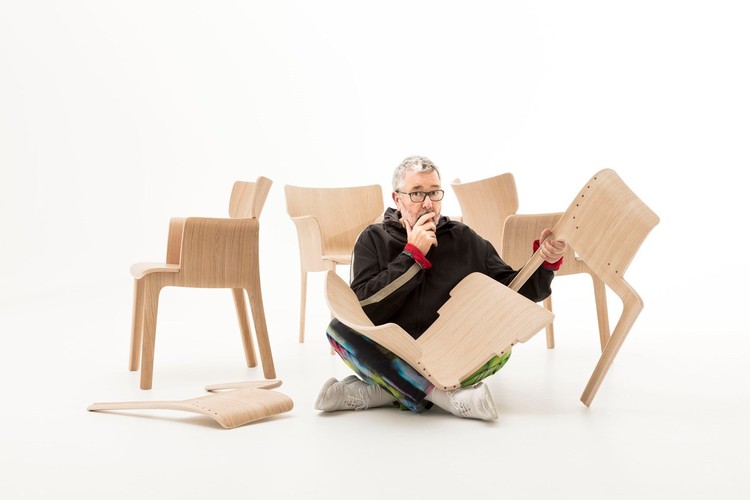
Believing that a creator has a duty towards society, Philippe Starck, is a multifaceted designer whose projects span across many disciplines. From architecture and interiors to industrial and furniture design, Starck’s portfolio is always, as he puts it, “focused on the essential”, and “must improve the lives of as many people as possible”. Author of Alessi’s famous lemon squeezer, he is known for pushing the boundary of design in everyday objects.
With 10,000 creations, completed or yet to come, Philippe Starck is a pioneer in “making things in the way of ecology”. In fact, ArchDaily had the chance to meet the designer at the 2021 Salone del Mobile, to discuss his design approach and visions as well as hislatest plywood creation for Andreu World.