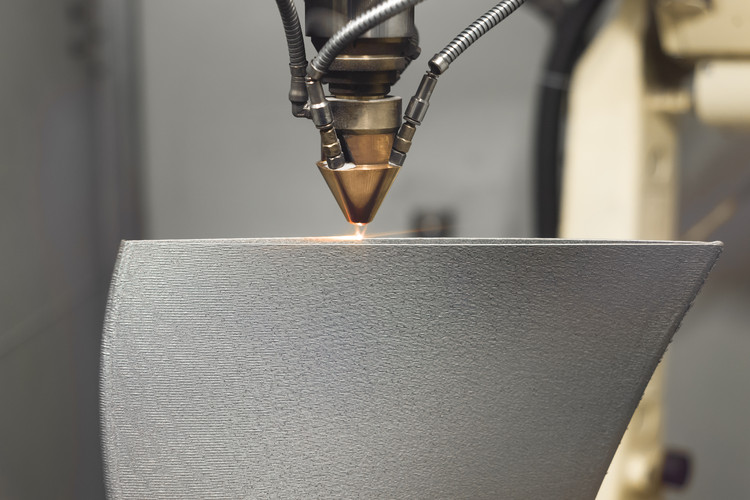
Additive Manufacturing (AM) is a term used to identify the manufacturing processes performed by 3D printing through layer-by-layer construction. In addition to avoiding the generation of waste through the use of precise geometries and exact quantities of material, these controlled processes can be much faster than traditional ones, since they don't require tools or other instruments.
Additive Manufacturing is done based on a digital model. The process begins with a CAD design or three-dimensional scan and then translates that shape into an object divided into sections, allowing it to be printed. Its use has extended from industrial design to the replica of archaeological objects to the manufacture of artificial human organs and tissues, among many others.
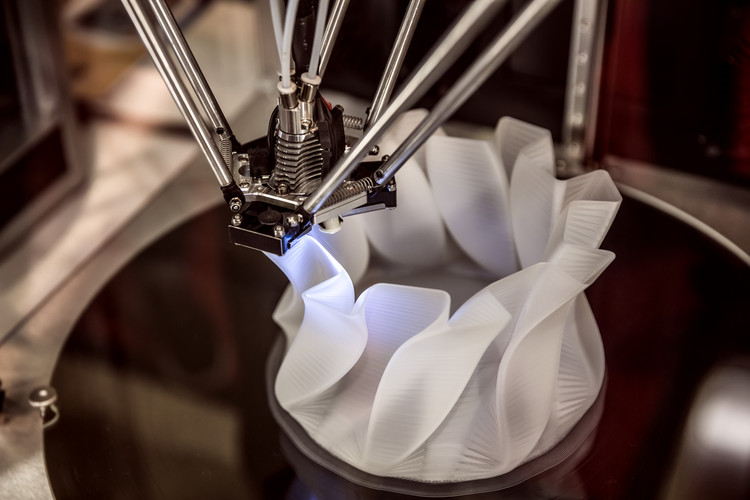
Although we have already seen some explorations that bring 3D printing closer to the construction of living spaces, they are not yet presented as an affordable option for massive application in larger-scale homes and buildings. However, it's important that we continue to familiarize ourselves with some of the technologies that could change the way we design and build the architecture of the future. Here are some of the most used additive manufacturing technologies.
VAT Photopolymerisation
Plastics, Polymers
In this process, the object is constructed layer-by-layer using liquid photopolymer resin, hardening the material with ultraviolet (UV) rays. To form the next layer, the platform lowers one level at each pass.
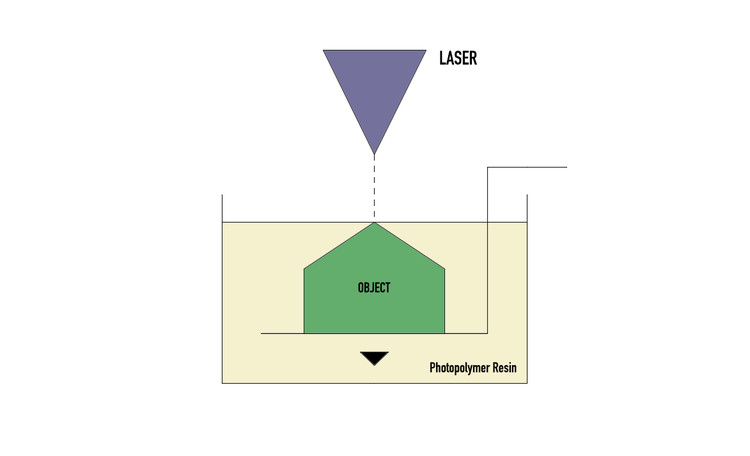
Fused Deposition Modeling (FDM)
Plastics, Polymers
"Molten" material is deposited in layers from the bottom up through a fixed nozzle that is at a higher melting temperature than the material, hardening immediately after depositing it. The support material, which allows the object to not collapse before being finished, is removed once the piece is done. It's advisable to use support materials that are easy to remove, such as water soluble PVA.
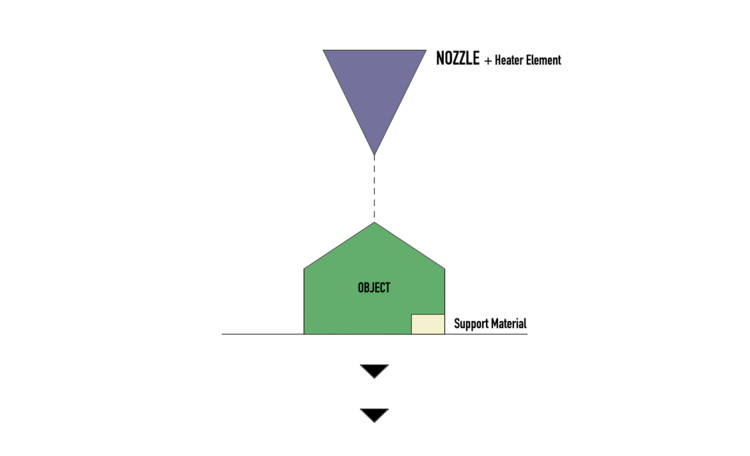
Material Jetting
Plastics, Polymers
UV-solidified photopolymers are also used in this technique. However, the liquid mixture of material (including the construction material of the piece and the support material), is injected in drops on a platform to form the shape of the element.
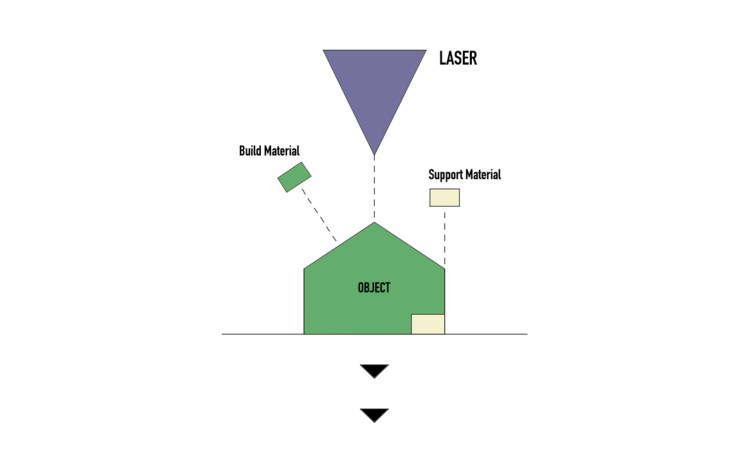
Binder Jetting
Polymers, Metals, Ceramics
Layer by layer, this system deposits liquid binder to combine with other dust particles, usually metallic, ceramic, or sandy. After the first layer, the platform lowers to allow the roller to add more dust, repeating the process until the designed part is completed.
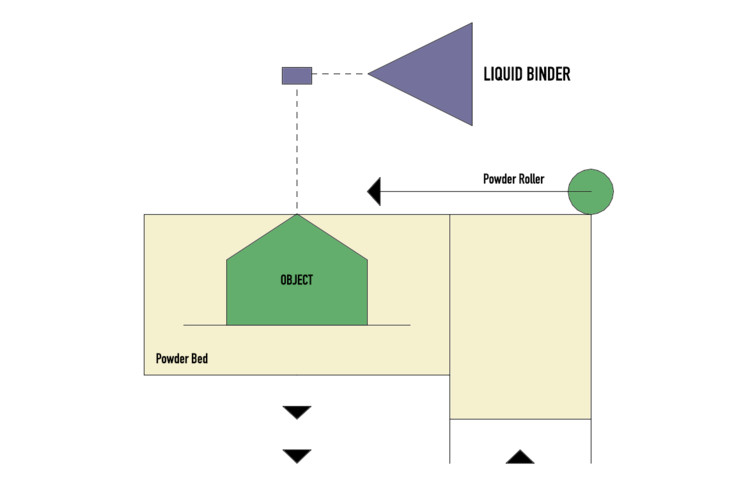
Powder Bed Fusion
Polymers, Metals, Dust-based materials
In this case, a thin layer of material dust is deposited by a roller over the work area and then melted, fused, and sintered through a laser or electron beam. The remains of the dust, which are not part of the final piece, are removed at the end of the process.
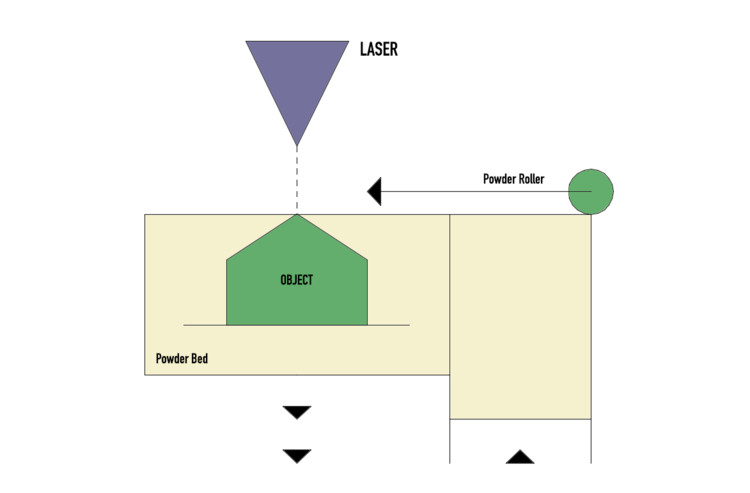
Sheet Lamination
Plastics, Paper, Metal Sheets
Plastic, metallic, or paper sheets are joined through ultrasonic welding or adhesive and then cut into the shape of the piece layer-by-layer. The ultrasonic welding emits a wave over the different sheets, located one above the other, heating their molecules to melt them. At the end of the process, the unified material is removed.
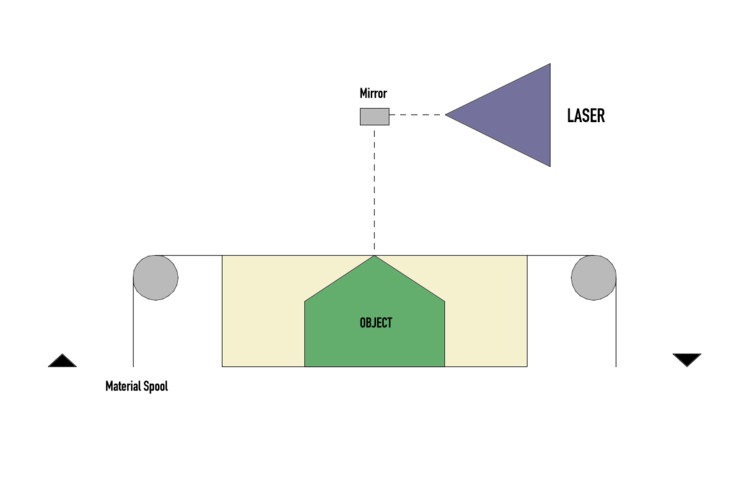
Directed Energy Deposition (DED)
Metals
In a process similar to that of Fused Deposition Modeling, the machine deposits molten material on the platform and then solidifies it with a laser or electron beam. In this case, the nozzle has freedom of movement, allowing the material to be deposited from different angles and positions.
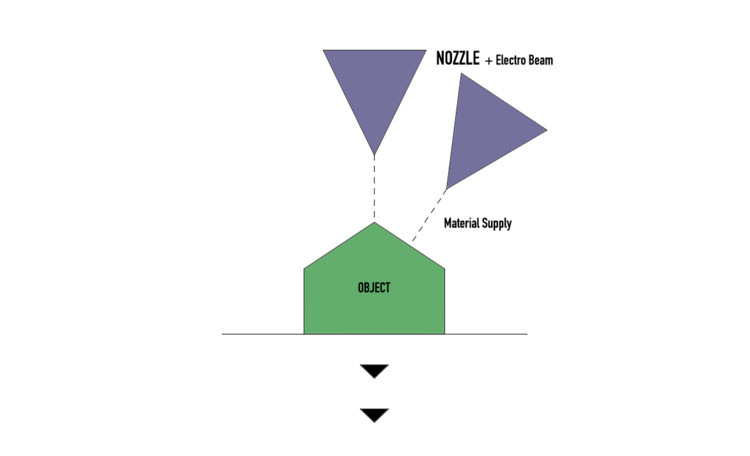
- Related article
Could 3D Printing be the Future of Social Housing?
Find more detailed information on each of these processes, consult the research conducted by Loughborough University.