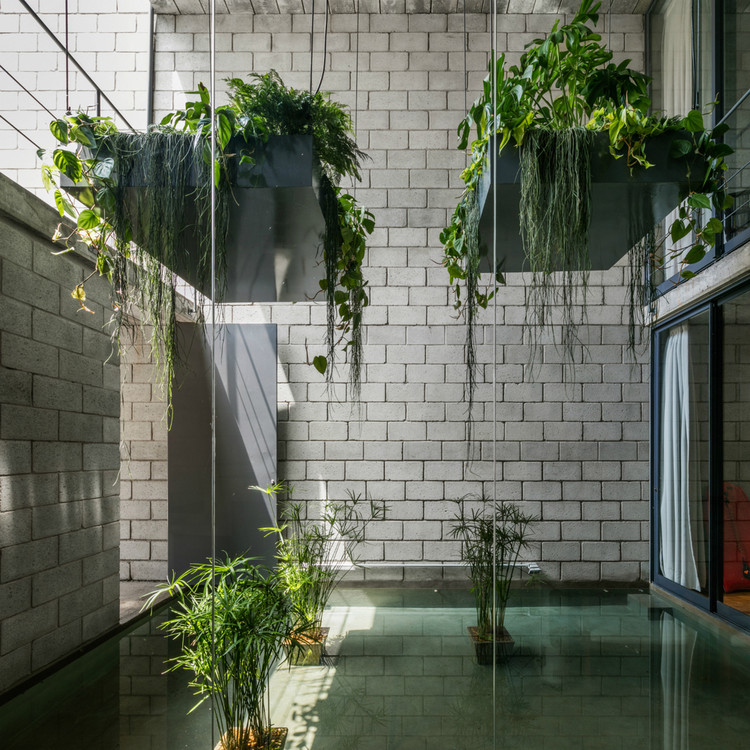
Concrete blocks are prefabricated materials primarily used for constructing walls. Similar to bricks, these blocks are stacked together and bonded with mortar, typically composed of cement, sand, and water. They are hollow inside to accommodate steel bars and mortar filling.
These blocks are available in a variety of dimensions and textures, ranging from traditional smooth surfaces to fluted or rough finishes. Additionally, there are special units designed for corners or beams with longitudinal reinforcements. The dimensions vary, from the classic 8x8x16 inches (approximately 19x19x39 cm) intended for structural use, to a size of 8x3.5x39 inches (approximately 19x9x39 cm) for partitioning walls. How can we creatively incorporate them into our designs?
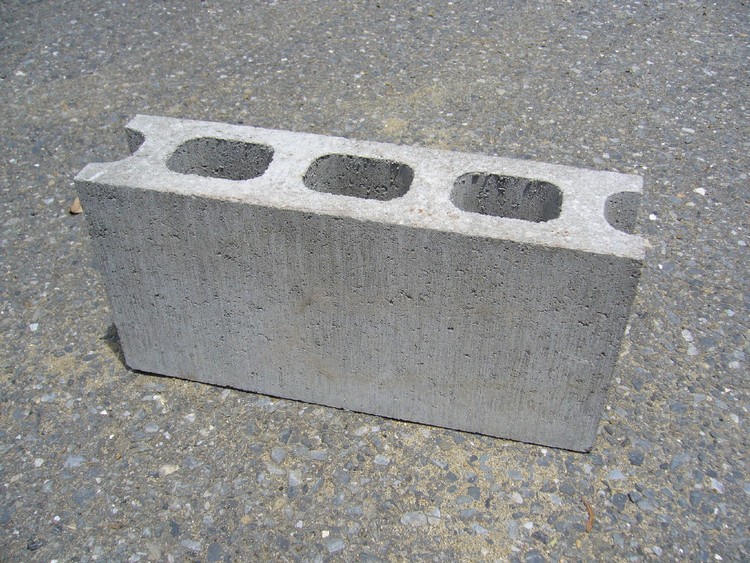
Although the first blocks—mass-produced in the early 1900s—were handmade, modern production methods are automated, allowing for the creation of thousands of blocks per hour. Moreover, since they do not require firing, each unit can be fabricated on-site by unskilled masons.
In terms of thermal performance, a block wall can function effectively with the appropriate measures in place. For instance, it's essential to ensure the correct placement of the mixture in all joints to prevent thermal bridges. Additionally, insulators such as EPS or Glass Wool, along with Polyethylene as a vapor barrier, can be incorporated into the interior of the blocks for use as exterior insulating plaster.
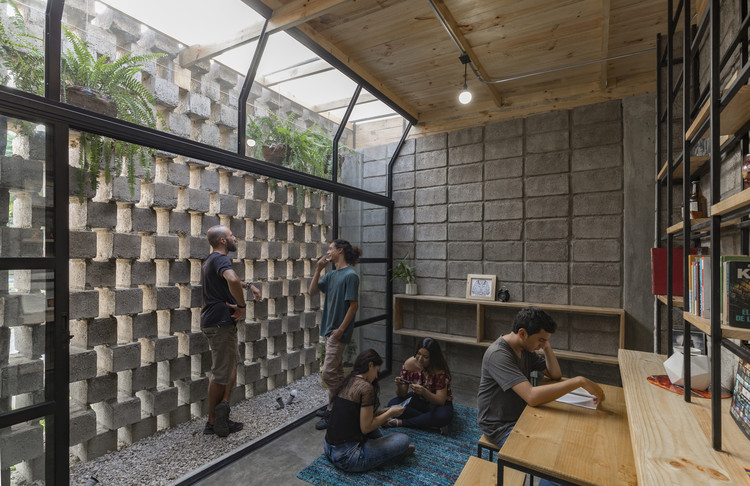
Broadly speaking, its manufacturing involves four processes:
- Mixing: After weighing, the appropriate amounts of water, gravel, and dry cement are mixed, followed by the addition of water.
- Molding: In specialized machines, the mixture is compacted into molds that define the shape, size, and exterior texture of the blocks. Mechanical vibrations typically aid this process.
- Curing: The blocks are placed in steam ovens (either low or high pressure) to facilitate hardening.
- Cubing: Once dried, the blocks are stacked into cubes for storage.
"The concrete commonly used to make concrete blocks is a mixture of powdered portland cement, water, sand, and gravel. This produces a light gray block with a fine surface texture and a high compressive strength," as the creators of the website How Products Are Made stated. Therefore, the blocks possess good mechanical capacity, are non-combustible, and offer acoustic insulation.
.jpg?1519415724)
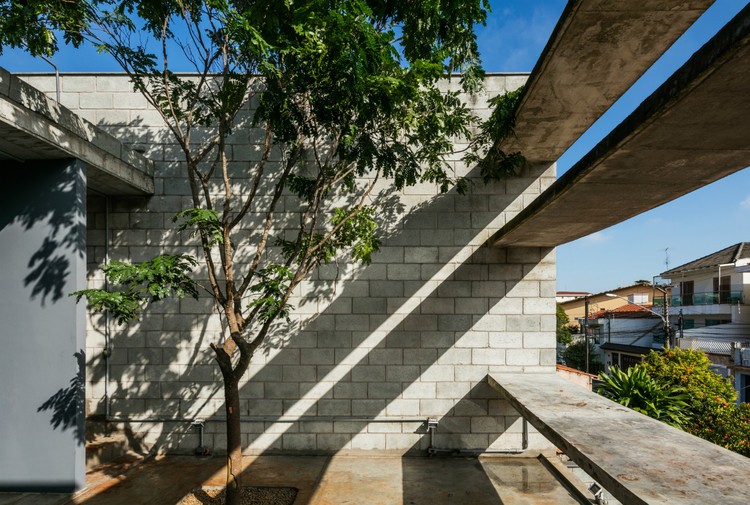
The basic concrete block has evolved to offer more comprehensive solutions, including waterproofing. Some contemporary models incorporate additives into the mixture to enhance the block's surface tension, thereby impeding the passage of water. Additionally, there are blocks designed with different edges to redirect water away from their surface.
Basic Construction
Before starting, you should consult local building codes and standards.
1. If using a strip footing, it should be twice the width of the block. Reference lines can be marked with thread or chalk, and a dry run without mortar should be performed.
2. Prepare the mortar and spread it onto the previously moistened strip footing, covering the width of a block. The initial layer should be 1 inch (2.5 cm) thick.
3. Begin placing the blocks starting from the corners, applying mortar to their vertical joints as you go.
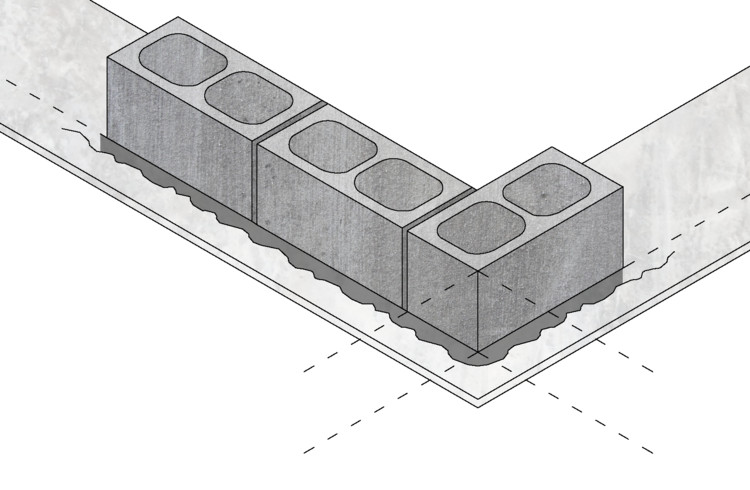
4. After completing each row, ensure the blocks are aligned both vertically and horizontally. Adjust as necessary by tapping them into place. Repeat this process for all designated walls.
5. As the holes in each unit align, they create a continuous vertical cavity where metal reinforcements can be inserted.
6. Once the mortar has hardened enough to hold a footprint, finish and smooth the joints, removing any excess mortar.
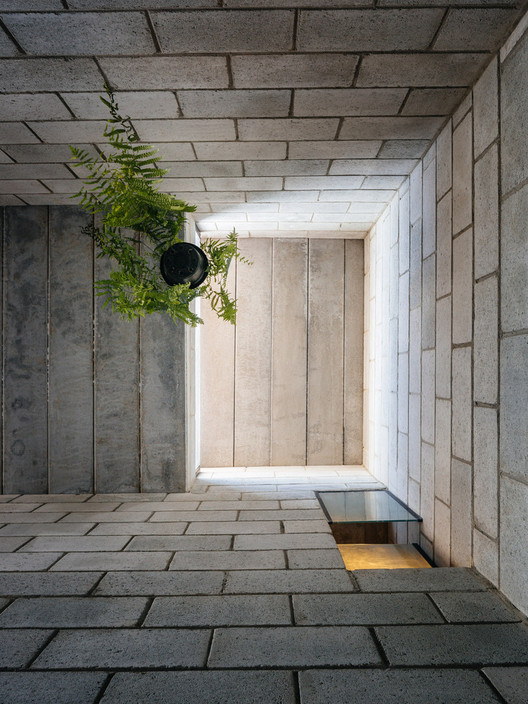
Architectural Design
Despite being a widely used material worldwide, its design possibilities have not been fully exploited. Concrete blocks are often associated with self-construction and low-cost housing, limiting opportunities to explore beyond functional design.
Through impeccable craftsmanship, the projects of architects such as Terra e Tuma, Natura Futura, Agustín Lozada, and Takao Shiotsuka Atelier invite us to explore new ways of utilizing concrete blocks. In their work, these blocks emerge as the protagonists of spaces, left exposed to reveal their original color and texture, distinct from traditional bricks. While more raw in appearance, they prove highly adaptable, complementing other materials and elements such as vegetation and water. By embracing this material, these architects have successfully reduced project costs without compromising spatial or architectural quality.
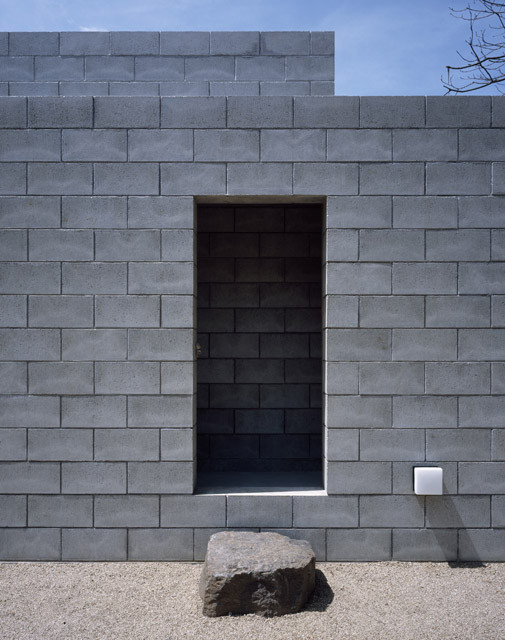
What other design options arise? The standard dimensions and modular nature of concrete blocks allow for easy design, similar to building with "legos", enabling the creation of topographies that can form furniture or variations in elevation. By rotating their original position, the perforations in the blocks can create permeable walls. These are simple ideas that can deliver effective solutions without being unaffordable.
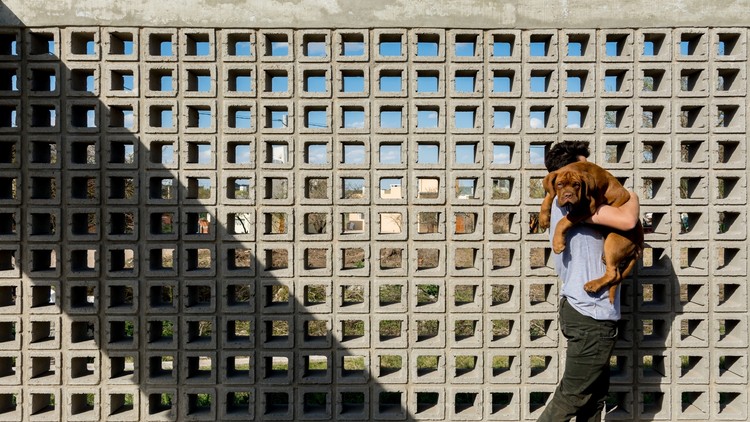
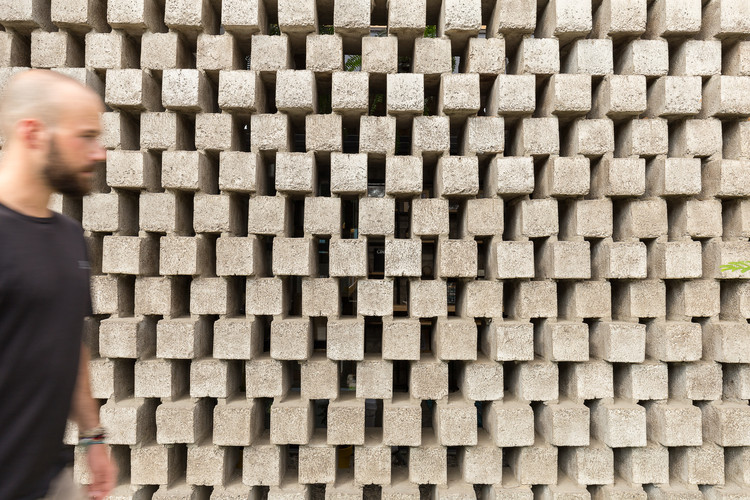
If you have worked with this material, we invite you to share your experience in the comments section below.