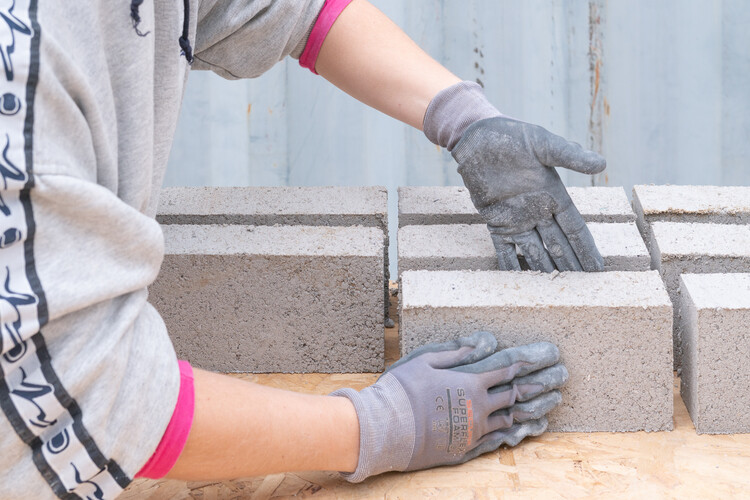
There are several symbols that transcend language barriers and are easily recognized and understood by people from different cultures. Examples include the male and female bathroom icons, the cross symbolizing health, and the universal Wi-Fi symbol. Among these universal icons is the recycling symbol, conceived in 1971 by Gary Anderson, an architect and designer who was a student at the University of Southern California. Depicting a continuous cycle, it is a triangle with three arrows arranged clockwise, each of which represents the industry, consumers and recycling.
Central to the concept of the circular economy is the reintegration of materials typically viewed as waste back into the production cycle. This concept is particularly important for the construction industry, which has historically depended on the destruction and extraction of resources in order to exist. In this case, nothing is more symbolic than the brick, which not only represents the construction of new things, but is also the perfect example of how to apply the concept of circularity. Creative minds have embraced the challenge of circularity, devising solutions that transform discarded materials into high-value resources and generating a wide range of products, using raw waste materials that range from seaweed and plastics to human hair. These innovations not only address pressing environmental issues but essentially redefine the way we build and inhabit our spaces. In this article, we highlight seven initiatives that are turning waste into bricks.
Turning Invasive Algae Into Housing
The invasion of non-native seaweed along the Mexican coast led local communities to organize beach clean-ups, as the malodorous invading species began causing respiratory problems among the population. Omar Vázquez Sánchez, the founder of Blue-Green in Puerto Morelos, saw an opportunity to repurpose this natural resource as a primary building material. After six years of conceptualization and experimentation, he successfully built a house using seaweed mixed with adobe.
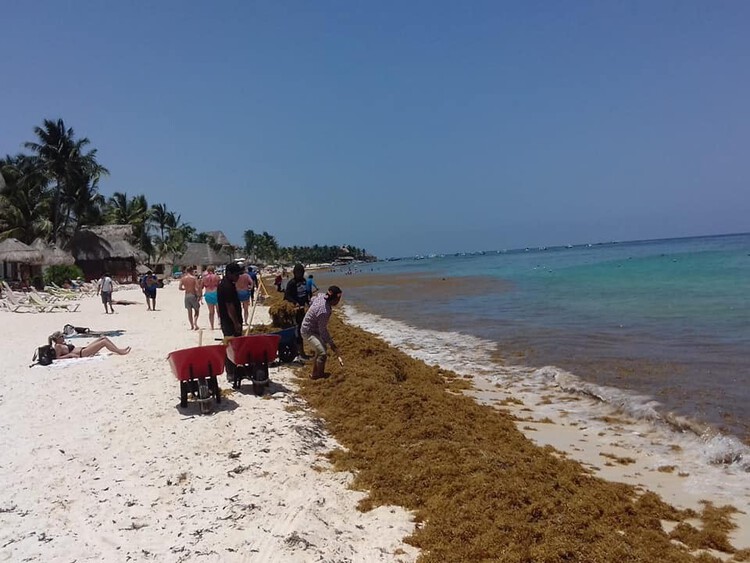
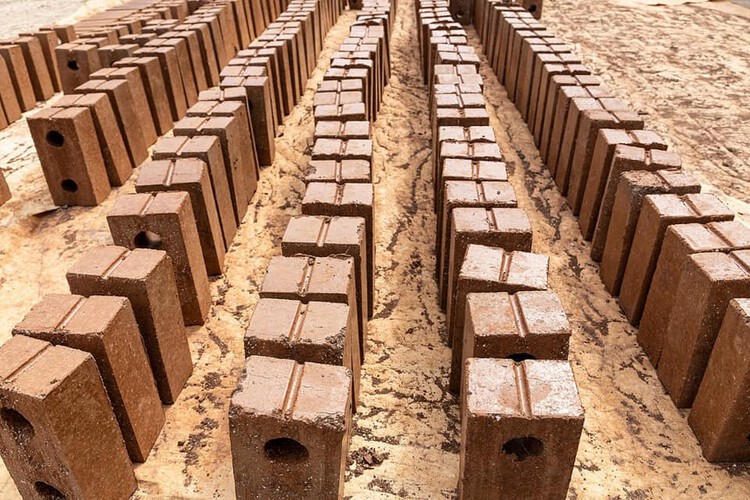
The incorporation of Sargassum seaweed into bricks has shown remarkable resilience, evidenced by its ability to withstand seismic activity and hurricane winds, confirmed by tests carried out by the National Autonomous University of Mexico (UNAM). Sargablocks are produced by crushing two main components: clay (from construction sand waste) and seaweed. A small residence, completed in just 15 days, consumed 50% fewer resources than a conventional social housing unit, and stands out especially for its high thermal inertia, allowing heat to accumulate during the day and be released at night. The founder's goal is to make this building material available for affordable housing construction for low-income populations, while also being suitable for higher-budget buildings. The bricks would therefore transform an environmental problem into a valuable, truly sustainable raw material.
Urban Waste for a Museum Façade
For the renovation and expansion of the Design Museum Gent, an innovative recycling process is transforming broken concrete and glass waste into bricks that will cover its façade. The material accounts for only a third of the embodied carbon of a traditional brick, due to the way its components are obtained and the fact that it doesn't need to be burnt. Gent Waste Brick will be used on the façade of the museum's expansion, which was designed by Carmody Groarke, and was developed in partnership with TRANS architectuur, materials designers BC Materials, and Local Works Studio. To achieve this, a method was created to grind construction waste materials combined with lime to form dry, cured bricks.
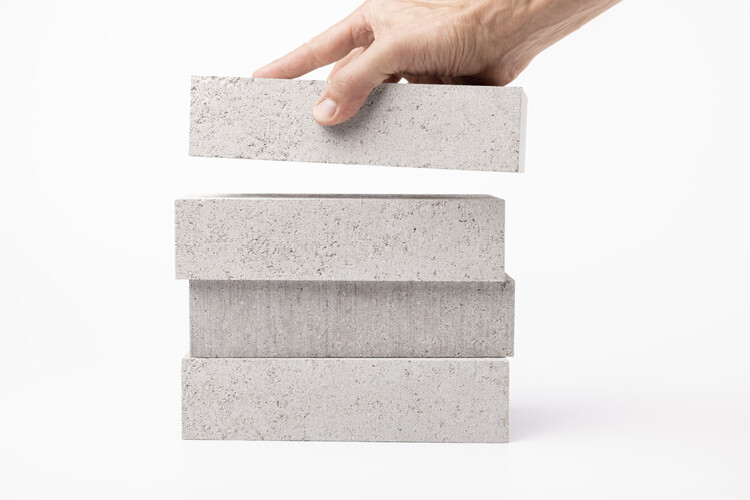
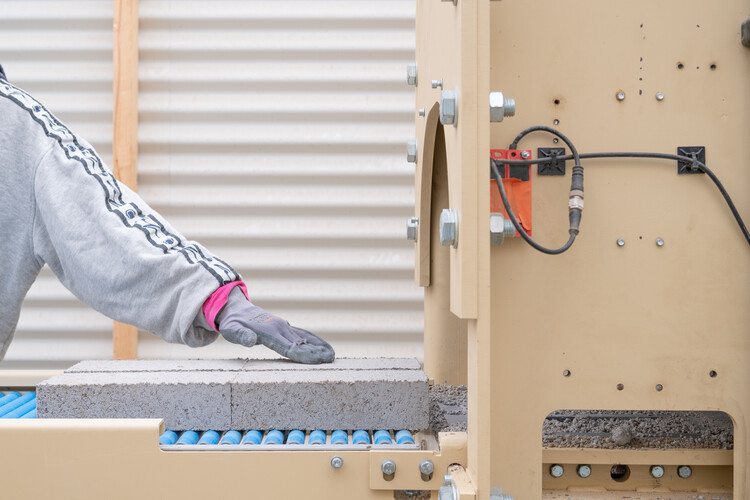
Made mainly from crushed concrete, masonry and glass from demolished buildings, the block uses materials collected mainly within a five-mile radius of the museum. The lime used as a bonding agent in the bricks comes from a slightly more distant area but is still regionally sourced. When combined inside a mobile processor the size of a shipping container, the raw materials are shaped into bricks which then undergo a dry curing process over 60 days. In contrast to conventional bricks, which are fired in a kiln once or even twice at high temperatures, Gent Waste Brick consumes significantly less energy. In addition, it absorbs carbon from the air during its curing process, sequestering carbon dioxide and becoming more resistant in the process. Over an estimated lifespan of 60 years, each brick will produce a third of the amount of CO2 of a conventional brick. They will be used on the outside of the museum's expansion, which is scheduled for completion in 2024.
Giving New Meaning to Plastic Waste
In Nairobi, Nzambi Matee, a Kenyan engineer, is leading an initiative that reveals the untapped potential of plastic waste. Her start-up, Gjenge Makers, seeks to convert discarded plastic into eco-bricks that are highly resistant, cost-effective, and have a positive environmental impact. Matee's conviction that plastic has value was born from observing the huge amount of plastic waste in landfills and public spaces in her city, a fast-growing African capital that generates approximately 500 tons of plastic waste every day, with less than 10% being recycled.
The technique developed to turn this waste into a building material combines crushed plastic with sand, forming a moldable mixture which, after exposure to heat, turns into a sturdy, lightweight block with advantages over concrete: sustainable bricks have seven times greater strength, are lighter, economically viable and ecologically beneficial. In addition, they cost up to 15% less to produce and, due to the fibrous nature of the plastic, air pockets are eliminated during the production process, resulting in great compressive strength and greater durability. Their inspiring work highlights the transformative potential of sustainable innovation in tackling environmental and social challenges.
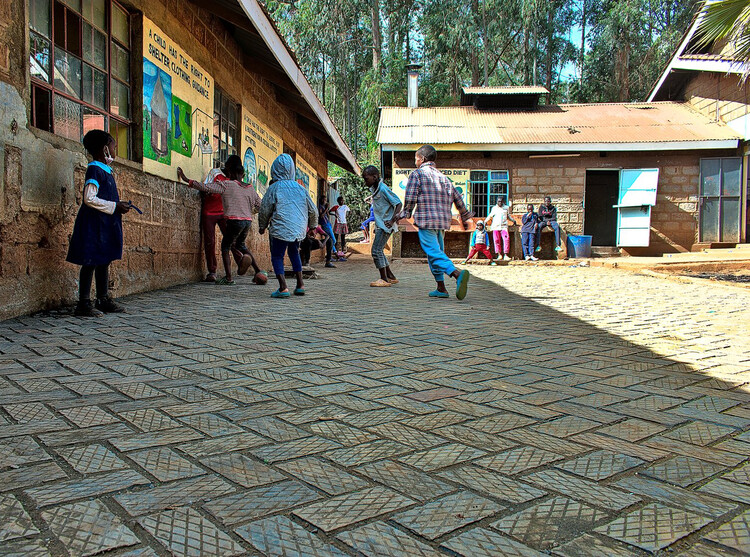
Another example comes from the Netherlands, developed by Precious Plastic. The innovative recycled brick solution addresses the challenges of plastic pollution and affordable housing. While plastic waste wreaks havoc on the oceans and the construction industry contributes significantly to carbon emissions, this brick offers a cost-effective and ecologically sustainable alternative. Produced with open-source recycling machines, each brick can retain 1.5 kg of plastic waste and is designed for easy assembly and interlocking, allowing for quick construction, even by inexperienced builders. These bricks are potentially useful for the construction of affordable housing, disaster shelters and public buildings, with an emphasis on their adaptability. Shared on Precious Plastic's platform as part of the #Openbrick movement, the initiative presents a promising way to combat plastic pollution, advance sustainable construction and meet global housing needs.
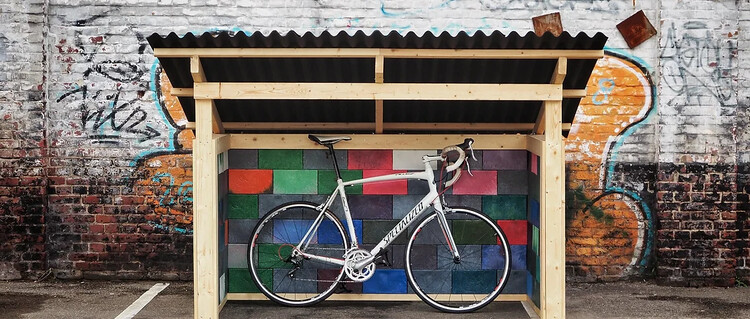
K-BRIQ®: Pioneering the Circular Economy in Construction
From the UK comes K-BRIQ®, produced by Kenoteq, which aims to redefine sustainable construction. It is a brick made from recycled inert materials in a low-carbon alternative to traditional masonry, adaptable to both interior and exterior environments. Compared to a conventional clay brick, it has a carbon footprint of less than 5% as it does not go through the firing process. In addition, around 90% of its content comes from recycled construction waste, and it doesn't require the use of cement (another villain of carbon emissions). The construction unit has a colored finish that requires no painting or surface treatment and has the potential for a variety of different colors using recycled pigments. The unit's performance characteristics and its "buildability" make it suitable for most applications normally reserved for traditional brick/cement products and historically unsuitable for air-dried products.
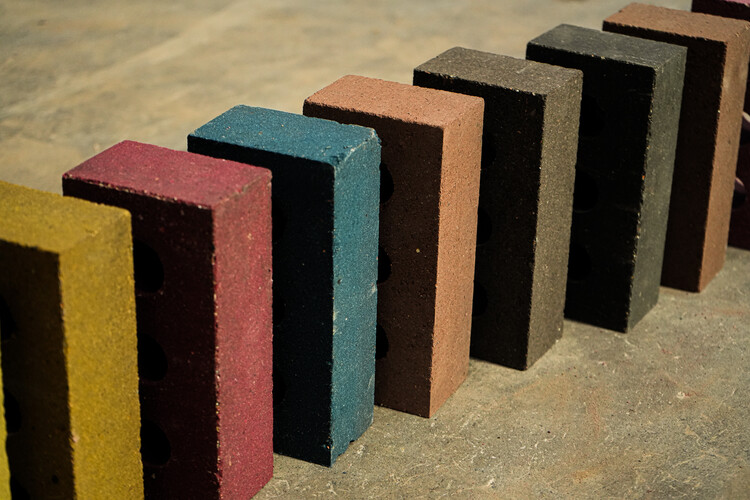
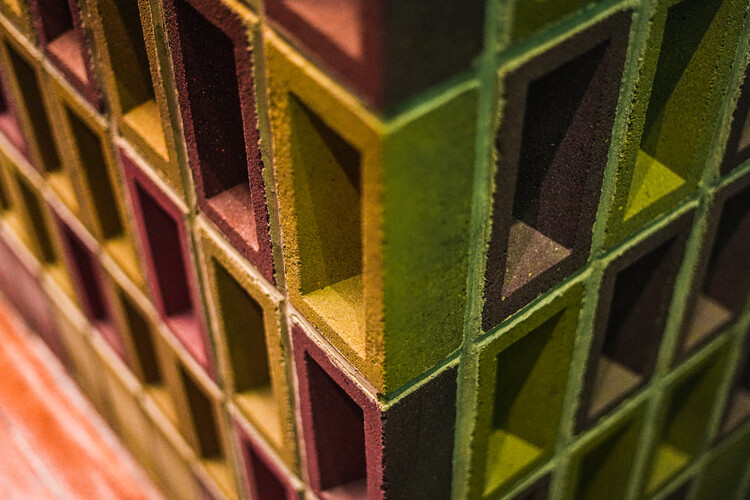
Certified by the BBA and backed by an Environmental Product Declaration, K-BRIQ® is available in a range of thirteen stock colors, all made from recycled pigments, and other colors can be achieved through blends. The product is in its final stages of BBA certification in the UK, allowing for its commercial use from late summer 2023. Its environmental product declaration (EPD) and design guide will also be available at the end of 2023, rounding up a year in which the company hopes to deliver 3 million blocks.
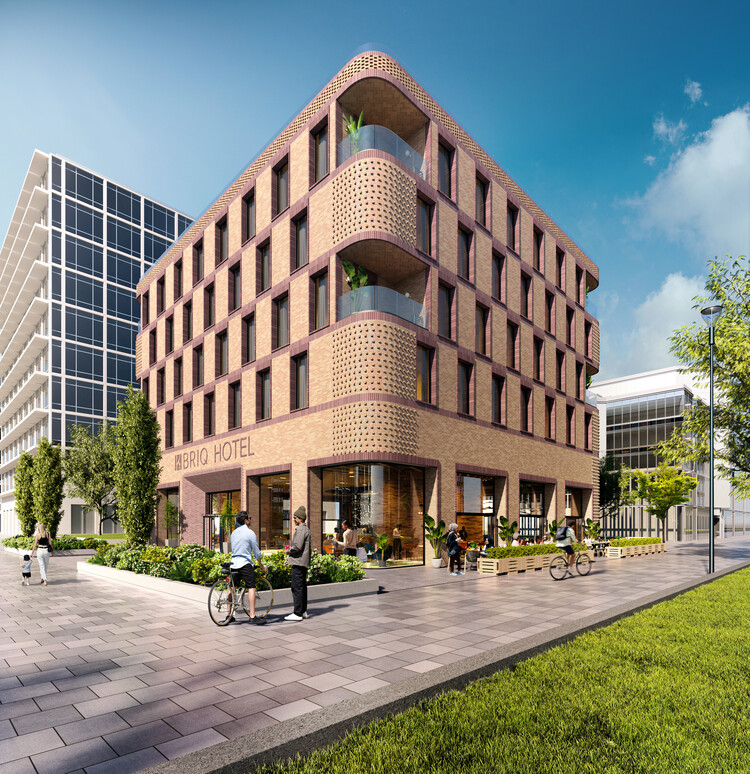
Using Industrial Waste
Pioneered by entrepreneur Manish Kothari, owner and managing director of Rhino Machines, Rhino Bricks offers a solution for brickmaking and the use of industrial waste. In contrast to conventional ceramics, which have a high environmental cost due to their manufacturing process and air pollution, these products are made up of 75% foundry dust and 25% recycled plastic. The previously unusable fine foundry dust finds new use as a crucial element in these bricks, while the recycled plastic acts as an effective bonding agent, replacing the need for water in the manufacturing process and further enhancing the bricks' ecological attributes. Rhino Bricks are 2.5 times stronger and 25% lighter than traditional bricks and their unique composition allows them to withstand greater pressures compared to conventional clay bricks, maintaining structural integrity even when subjected to drilling or splitting. In addition, they are manufactured very quickly, and can be ready for use just 30 minutes after production.
Raw material can also come from unusual places. Ellie Birkhead, a graduate of the Design Academy Eindhoven, has been developing ecological bricks through her "Building the Local" project. Her bricks are made using clay mixed with horse manure, glass bottles from a pub, wool, straw ash from a farm, spent grain from a brewery, and hair from a hairdresser. Yes, human hair. Her project revives the brick legacy of the Chiltern Hills, combating the impact of globalization on local industries. By incorporating materials specific to the region, Birkhead nurtures the link between architecture, aesthetics and culture, reinvigorating craftsmanship. Her venture echoes a wider call to safeguard threatened industries and skills, highlighting the urgency of preserving heritage in a changing world. "Building the Local" is a testament to creative sustainability and respect for local legacy, guiding us towards a more conscious future.
By redefining waste as a valuable resource, the construction industry is witnessing an ecological revolution driven by innovative minds. From the use of invasive seaweed to create resilient homes, to the transformation of discarded plastic into robust bricks, the circular economy finds expression in bricks that encapsulate environmental and social value, shaping attractive, durable, and affordable housing. As the world searches for creative ways to tackle global challenges, these stories of transformation inspire the adoption of responsible practices and the building of a more conscious tomorrow.