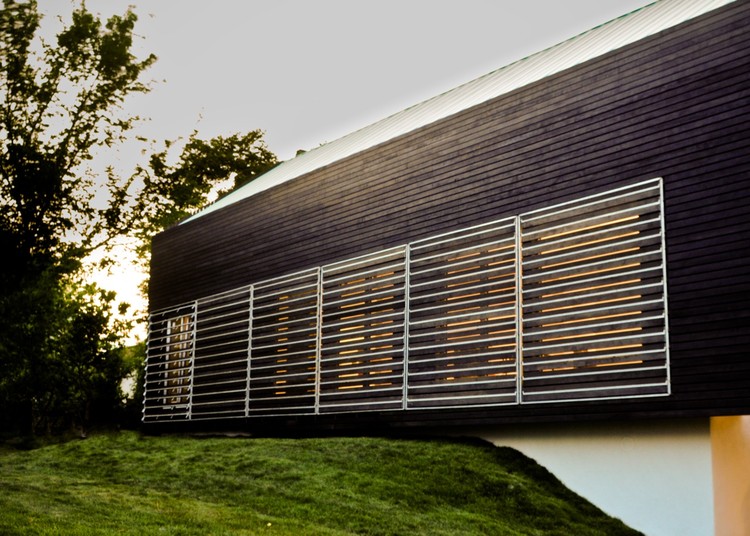
-
Architects: Studio 804
- Area: 1700 m²
- Year: 2010
-
Photographs:Studio 804
Text description provided by the architects. The Prescott Passivhaus is a single-family, low-energy residence located in Kansas City, Kansas. This unique house is designed for the affordable-housing market as a spec house that will sell to qualified buyers, those with an annual income of no more than eighty percent of the target Area Median Income (AMI).
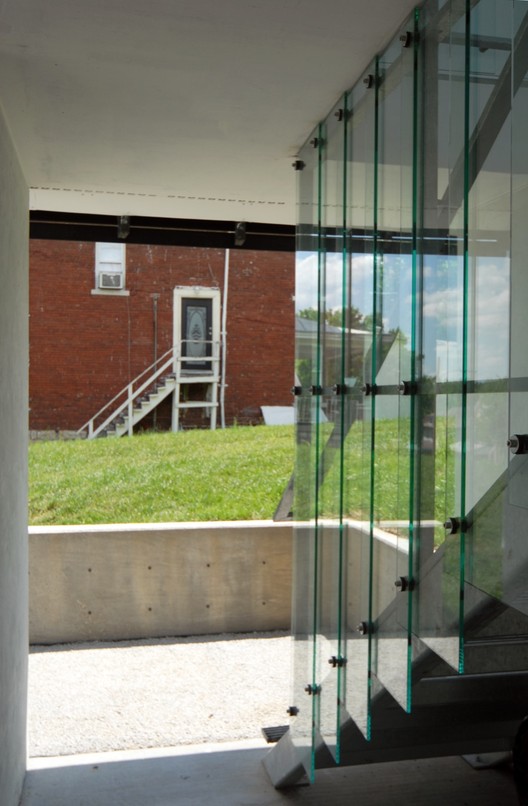
Designed to exceed both Passivhaus and LEED Platinum standards, the residence uses minimal energy through affordable passive means. The home is located in the Prescott neighborhood which, despite being just minutes from downtown Kansas City, remains a neighborhood in transition not unlike the rest of the derelict urban core that typifies the city.
This intriguing wood clad Passivhaus acts as a prototype for the region. It aims at being the first certified Passivhaus in the state of Kansas, and is one of only a handful in the country. To obtain its goal of a ninety percent reduction in heating and cooling energy demand, the house uses low-cost passive strategies such as louvers, thermal mass, high performance windows, super insulation, southern orientation, and an airtight building envelope. An energy recovery ventilator works in conjunction with these strategies to temper fresh intake air with energy from the exhaust air, providing constant fresh air year round.
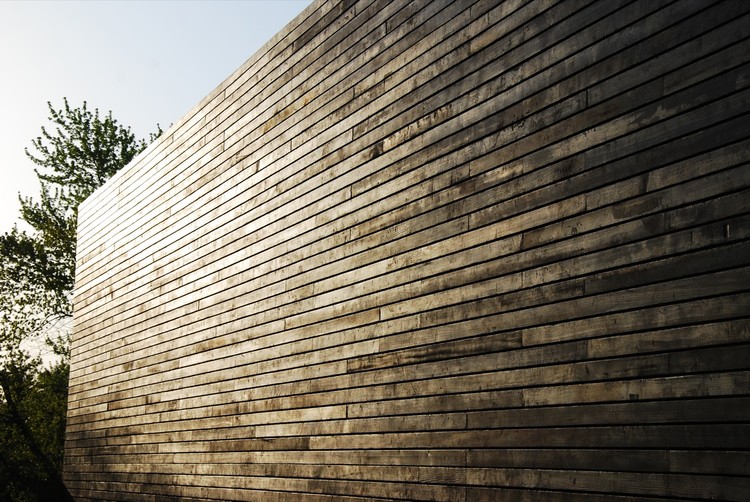
Under the guidance of the LEED Platinum criteria, measures were taken to ensure the sustainability of the Prescott Passive House in ways beyond merely energy efficiency. Site location and treatment, material content, construction waste management, and water efficiency were all carefully examined.
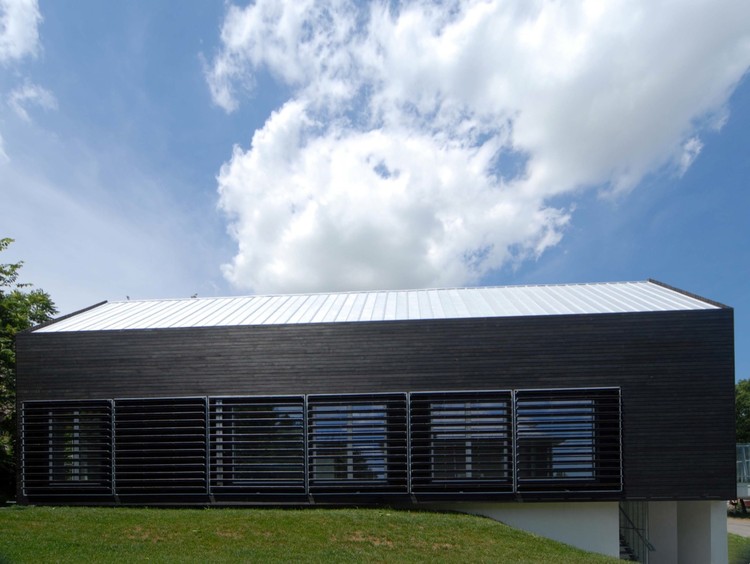
This 1,700 square foot, three bedroom, two bath residence bestows many amenities within a small ecological footprint. Despite its modest size, the open floor plan creates a surprisingly spacious interior. A double height living room connects the main floor with the upper level, where the master bedroom is located. The stacked master bathroom and main floor bathroom are flooded with natural light through an internal two-story frosted glass wall across from the expansive southern glazing. Overlooking the living room and southern array of windows is the flexible loft space. On the main level, the living room is connected to the kitchen and dining spaces with an exposed concrete thermal mass floor. These living areas are located just off of the 400 sf deck, which lends uninhibited views of the Prescott neighborhood and the Kansas City skyline while doubly functioning as the carport roof. At the west end of the main level are two additional bedrooms with views to the surrounding double width lot. Remote controlled operable skylights create the only break in the northern envelope of the house, and operable glazing stretches the entire length of the southern side to encourage natural ventilation. This impressive façade is protected by louvers optimally angled to allow winter heat gain yet block sunlight from penetrating the house in the summer. Downstairs, a full walkout basement provides ample storage as well as a finished flex room located directly off of the carport.
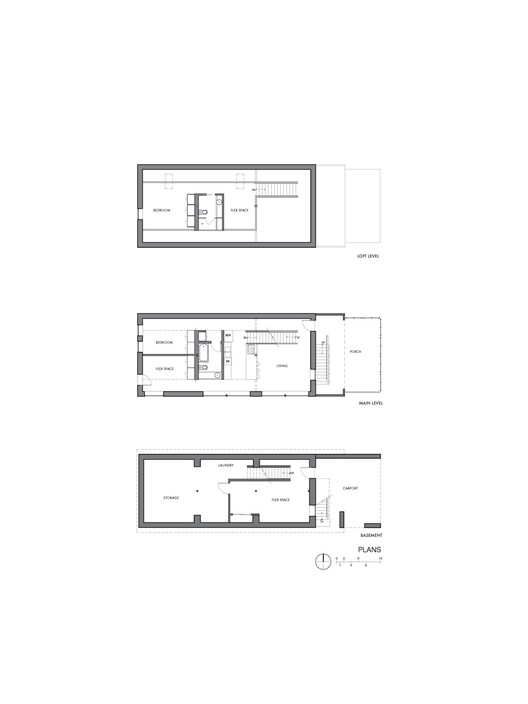
A sixteen inch thick insulated wall assembly and a twenty-two inch thick insulated roof assembly provide the basis for a home that seeks a ninety percent reduction in heating and cooling energy. This airtight assembly nearly eliminates all heat transfer through the building envelope, keeping all heat gained from the high performance glazing within the house. The energy recovery ventilator and thermal masses seek to further maintain a constant interior temperature, reducing most needs for additional tempering support. Outside, clotheslines discourage the use of an electric clothes dryer, one of the least efficient of the house’s appliances, all of which have received the Energy Star rating.
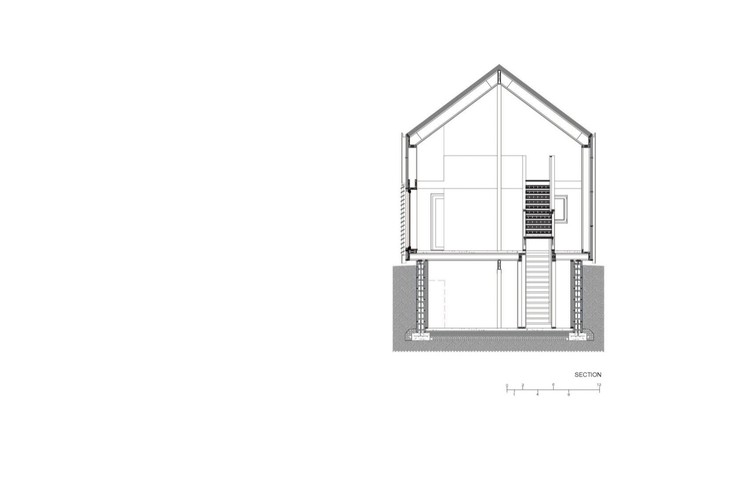
Due to Passivhaus strategies, engineered wood was the only choice for framing. The entire house was framed in engineered lumber. The width of the TJI joists allowed for the wall (12”) and roof (16”) depths needed to house the thick cellulose insulation required for Passivhaus. In addition, the creation of a primary structural system to carry the ridge load through columns to the foundation was accomplished with Laminated Veneer Lumber (LVL). This enabled the space to remain open, so all rooms could be filled with natural light, a principle tenet of our energy-saving concept. We could not have achieved our design goals without the use of engineered lumber.
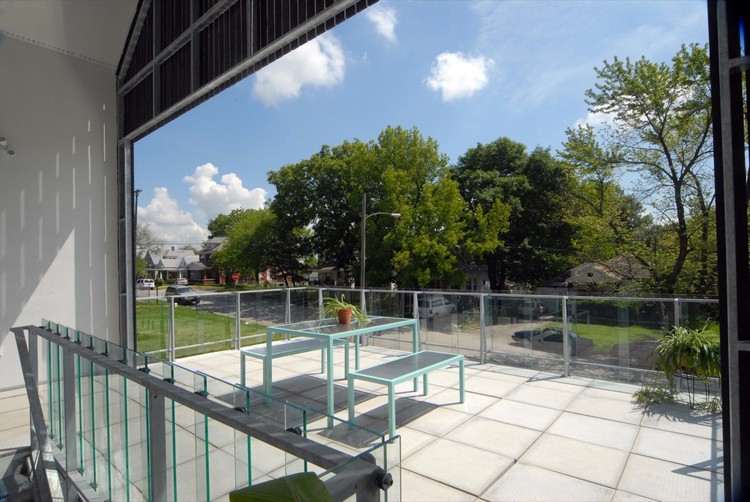
In the spirit of the age-old Japanese shou-sugi-ban tradition, the exterior of the Prescott Passivhaus is clad in a charred Douglas fir rain screen. This low-maintenance assembly yields a UV-protected dark black finish to the house. Recycled paper windowsills and countertops, bamboo flooring, and a concrete, thermal mass-providing floor complement the clean white interior walls and ceiling.
Being the first new construction in its Kansas City, Kansas neighborhood in many decades, the Prescott Passive House breathes new life into an established neighborhood. With its sustainable energy conservation strategies, the home has further served as an educational tool to the community throughout the construction process.