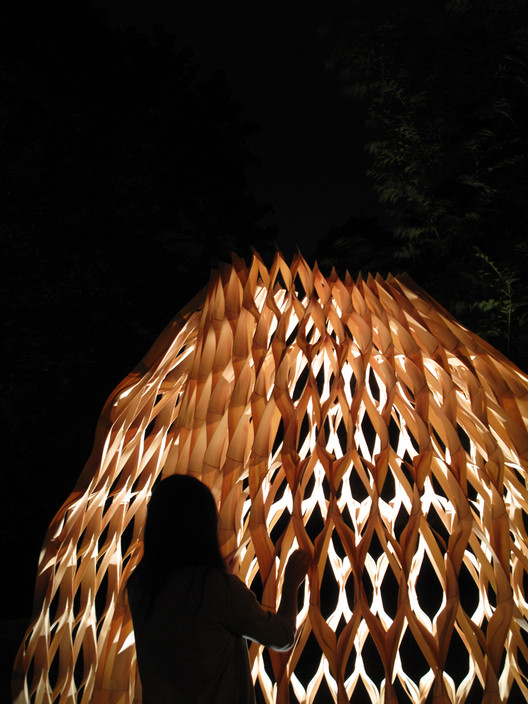
Wing Yi Hui and Lap Ming Wong, two students from Hong Kong studying at The Oslo School of Architecture and Design, have shared their wooden pavilion with us. The performance-oriented design studio, under the guidance of Professors Michael U. Hensel, Defne Sunguroğlu Hensel and Dr. Birger R. Sevaldson, gave the students the opportunity to explore the performance of the wood and create a “customization possibility” within the constraints of a “platform of standardization.” The designers explained, “By understanding the performance of material, and allowing it to perform its intrinsic properties, innovative and sustainable methodology of architectural production could be emerged as a natural response. Deformation of wood due to moisture is no longer a nuisance but a benefit to fabrication.”
Check out their process work and even more about their project after the break.
By researching the properties of the wood, the designers could make the wood conform to their artificial aesthetics in a natural way. “During the process of swelling, pressure difference among cells results in energy storage within the micro structural system. By applying lamination constraints to the curved veneer before the rebound upon drying, energy can be stored. Through testing the process of lamination and deformation, specific system with highly variable geometry can be explored,” explained the designers.
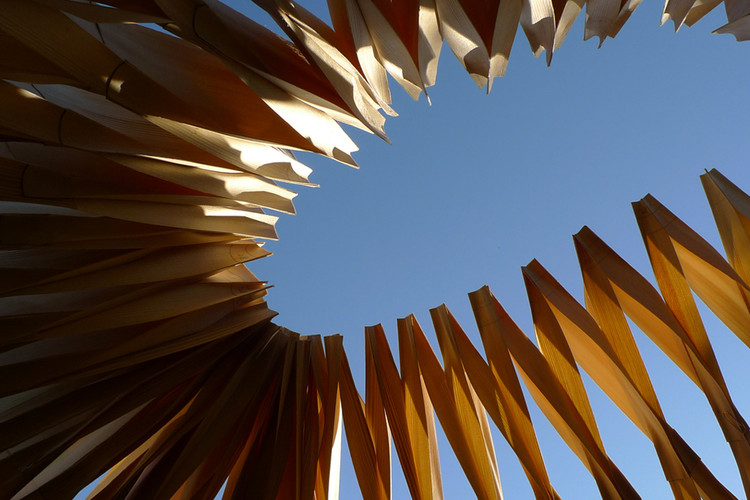
To reach the desired affect, the process was a constant experimental exercise using both digital and physical methods. Relying on digital computations alone does not yield completely accurate results, for the complex structural arrangement and performance of wood may add some varying affects. “The computational tool predicted the approximate dimensions, global geometry and compositional curvature while physical tests are carried out to combine the material performance with computer-generated data for further evaluations…The relationship between the tools create unique interface for generation of the emergent typologies and global geometry of performance-oriented exploration as such,” explained the students.
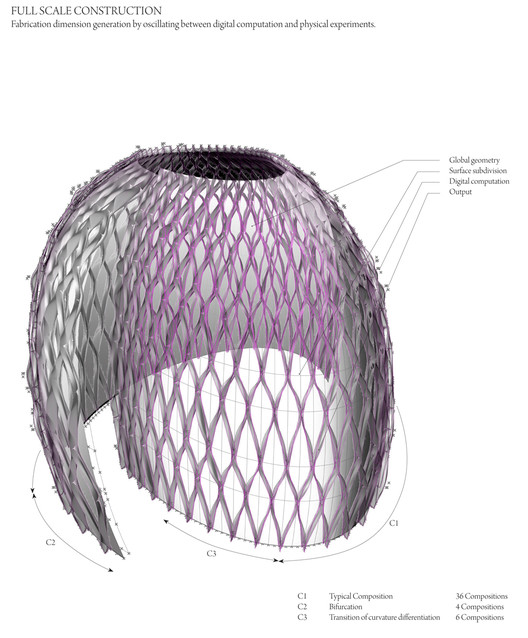
As the project developed, the students applied their understanding of strategic moisturization, the translucent qualities of thin veneer and elasticity of wood to create “a potential architectural element.” The construction consisted of 46 groups of components while each of them consisted of 5 components: 36 identical groups of them are fabricated for the major structure, while 3 components in 6 groups of the total are fabricated differently for extreme curvature shift. ”Adding components and varying lamination position and area creates significant internal self-organization of the system and generate highly differentiated geometry.”
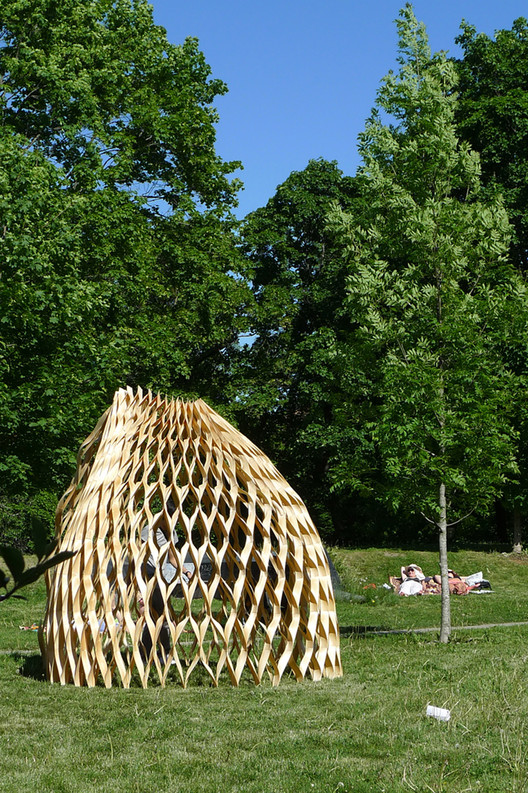
Rather than resorting to computational machines for the fabrication process, by simply varying the parameters of lamination in terms of positions and area, the curvature of the wood changes. ”Standardized and identical components are then performing with customized post-construction alterations without fabrication of unique components or pre-shaped elements. Standardization could actually achieve customization in the research without production large amount of waste,” added the designers.
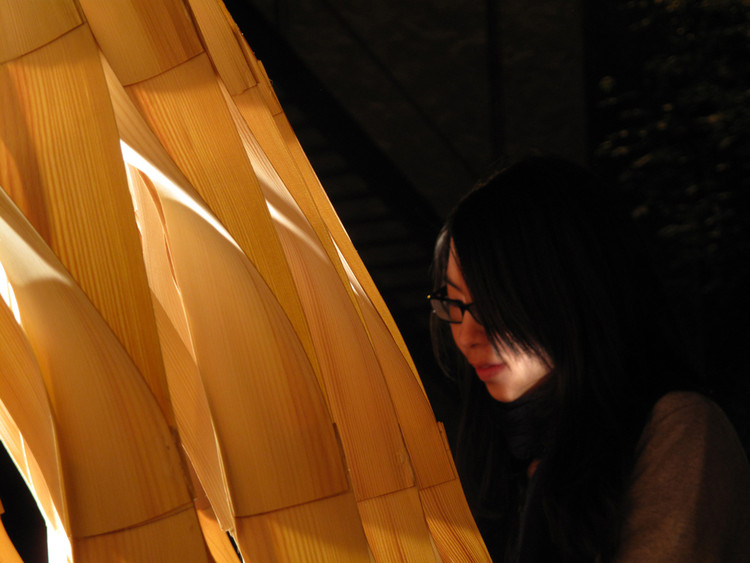
Performance-oriented design: Wood Pavilion Students: Wing Yi Hui, Lap Ming Wong from Oslo School of Architecture and Design Performance-oriented design studio, Conducted by: Prof. Michael U. Hensel, Defne Sunguroğlu Hensel and Prof. Dr. Birger R. Sevaldson.