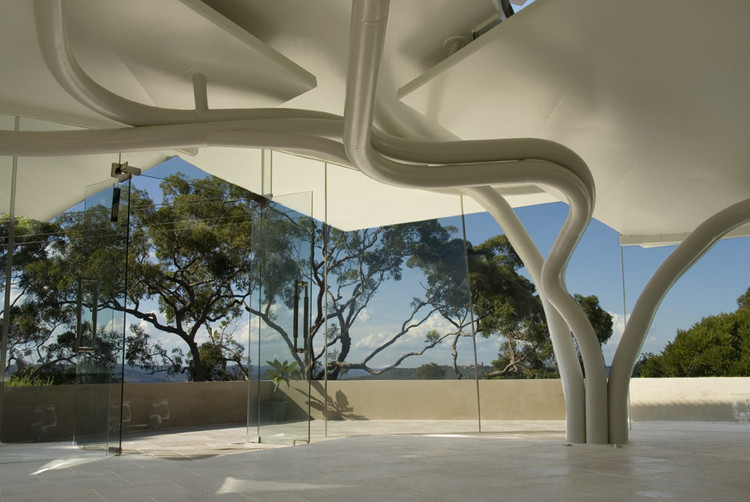
-
Architects: Undercurrent Architects
- Year: 2009
-
Photographs:Hugh Rutherford
Text description provided by the architects. Leaf House is building that allows users to be inside and in-the-garden at the same time. It is a self contained cottage forming part of a coastal residence in Sydney; a Pavilion for experiencing Nature.
The building integrates the environment and reflects qualities of the landscape: its canopy structure blends into the foliage; its podium base shapes the terrain.
The design is characterized by curved copper roof shells resembling fallen leaves and a vine-like structural system channelling dynamic growth inside.
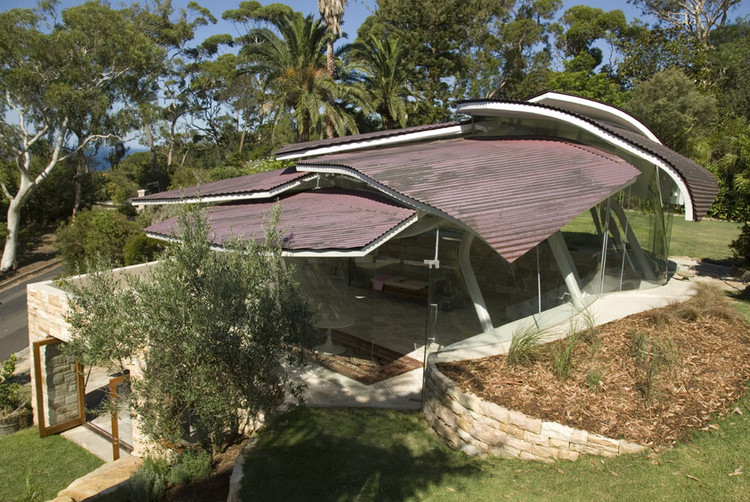
Daylight filters through porous roof shells onto a podium deck and the open plan living areas. Views and reflections subtly modulate the surrounding garden through an enclosure of moulded glass. Private spaces offer introspection inside the sandstone podium buried in the terrain.
The project entailed design and building roles as methods were improvised to achieve high technical complexity within cost constraints.